Digital and sustainable services throughout the machine life cycle.
- Remote Service: from machine support to platforms for spare parts management and training
- New digital solutions for pharma and food
- Sustainability as service focus for food manufacturers
Waiblingen, Germany – Syntegon Technology is far more than a machine manufacturer: Syntegon supports customers with solutions and services throughout the entire machine life cycle, as the specialist for processing and packaging technology demonstrates at the Virtual Show 2020 from May 7 to 13. The virtual event emphasizes Syntegon’s focus on its service portfolio. Amongst others, visitors will see how Syntegon will support them even better with intelligent and sustainable services in the future.
Remote Services for secure access from afar
Considering the current circumstances, Syntegon not only offers a virtual event, but also provides services from afar. Right now, many customers use Remote Services when they need assistance with machine settings or troubleshooting. Visitors of the Virtual Show can look forward to an exclusive offer for this specific service.
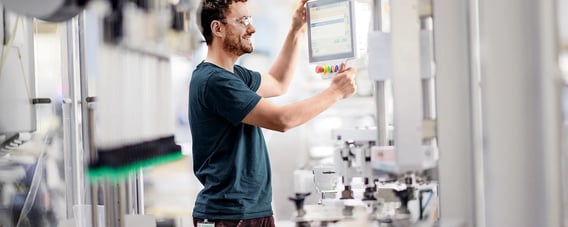
Syntegon Technology offers various remote services with secure remote access, including online operator training and the E-portal for easy spare parts ordering.
Reproduction for press purposes free of charge with credit “Picture: Syntegon”
Syntegon also provides further services and consulting offers, for which a Syntegon Technology employee would usually travel to the customer's site, via digital channels. For example, customers can order spare parts via the E-portal, Syntegon's online shop.
Operator training courses are also held virtually. Participants can choose the format according to their individual needs: Syntegon offers web-based and virtual reality training, as well as virtual classroom training on the online platform.
Digital services for trouble-free operations
Digitization also plays a major role in the production environment: pharmaceutical manufacturers benefit from the long-standing experience of Syntegon experts in developing and implementing software solutions. The Pharma i 4.0 Solution Platform, for example, provides plant operators with important OEE data and monitors the status of machines and processes. It also supplies real-time information about events such as alarms or machine downtimes.
/remote-services.jpg?width=568&name=remote-services.jpg)
After customers receive instructions via Remote Service from Syntegon's service experts, they can adjust machine settings accordingly.
Reproduction for press purposes free of charge with credit “Picture: Syntegon”
In addition to preventive maintenance, predictive maintenance will become increasingly important in the future: "Predictive maintenance makes downtimes foreseeable and ensures trouble-free production," explains Muhammed Ali Turac, product manager for digital services at Syntegon Technology. At the Virtual Show, the company presents MIRA (Machine Intelligence Reporting & Analytics) for the first time: thanks to intelligent algorithms, the modular software solution detects wear and tear on process-critical components such as fans. Up to six weeks before a potential failure, it announces that a component needs replacing. "The decisive advantage of this system is that it does not intervene with the machine controls. This means that retrofitted systems do not have to be re-qualified and validated," says Turac.
Syntegon Technology ensures trouble-free operations for pharmaceutical manufacturers with the patented Smart Skin Quantifeel™ system. It reduces downtimes by optimizing the transport of glass containers. Which points in the machine indicate particularly high stress on glass containers due to impact, pressure or rotation? Sensors identify critical processes, which can then be eliminated reliably. This results in fewer downtimes and less waste due to reduced glass breakage.
Efficient maintenance and optimized production with cloud platform
Thanks to the new, cloud-based Digital Shopfloor Platform, paper-based processes and unnecessary loss of time for maintenance work are a thing of the past in the food industry. "Technicians have their task planning as well as all manuals and documentations virtually in their pocket," says Sven Scharnitzki, product manager at Syntegon Technology. Using the interactive Performance Board with its intuitive interface, employees can see critical manufacturing data such as production time, losses and stops at a glance. They recognize optimization potential faster and can avoid downtimes. In addition, QR codes on the machines make sure that relevant data is displayed promptly and easily. This saves time and resources – and makes daily work easier.
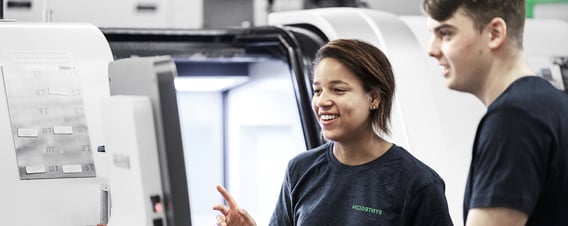
Thanks to the new, cloud-based Digital Shopfloor Platform, paper-based processes and unnecessary loss of time during maintenance work are a thing of the past for food manufacturers.
Reproduction for press purposes free of charge with credit “Picture: Syntegon”
Upgrade on sustainability
Sustainability is a particularly important topic in the food packaging industry. With the new PHS 2.0 sealing jaw technology, Syntegon now offers a retrofit kit for vertical bagging machines, which reduces film consumption while increasing production speed by up to 25 percent. Food manufacturers looking to test sustainable alternatives for their existing lines can now use Syntegon's material testing service. The service experts carry out tests on their own equipment so that customers do not have to interrupt their production. Detailed reports and recordings are then analyzed together with the customer.
About Syntegon Technology
Syntegon Technology is a leading global process and packaging technology provider. Formerly the packaging division of the Bosch Group, the company, headquartered in Waiblingen (Germany), has been offering complete solutions for the pharmaceutical and food industries for over 50 years. More than 6,100 employees at 30 locations in more than 15 countries generated a total revenue of 1.3 billion euros in 2019. The portfolio of intelligent and sustainable technologies includes stand-alone machines, as well as complete systems and services. Fields of application in the pharmaceutical industry are the production, processing, filling, inspection and packaging of liquid and solid pharmaceuticals (e.g. syringes and capsules). In the food industry, the portfolio includes process technology for confectionery as well as packaging solutions for dry foods (e.g. bars, bakery products and coffee), frozen foods and dairy products.