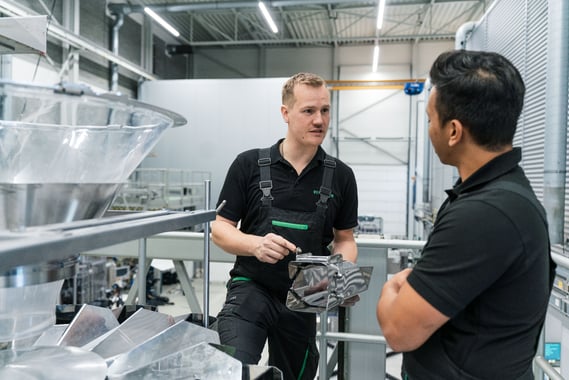
Service Agreements
Find out more about our Service Agreements here.
Visually appealing, cost-efficient, and extremely flexible: flow wrappers are the all-round solution for packaging food products as the variety of packaging options is almost limitless. Our portfolio includes various types of flow wrapper machines, from entry-level machines with an output of 80 packages per minute to fully automated, seamlessly integrated systems with output capacities of up to 1.500 packages per minute. Our systems are suited for a variety of products, including chocolate, biscuits and baked goods, bars as well as frozen food and solid goods such as detergent tabs. They are even able to wrap pharmaceutical products such as BFS cards or tablets in blisters. The efficacy of flow wrappers in these applications highlights their versatility.
Flow wrapping machines & features are enhanced by the gain of linear motors (XTS). Due to the high flexibility offered by flow wrappers is becoming increasingly important in the confectionery industry, Syntegon recognized the potential of XTS technology from Beckhoff early on. The Syntegon team in Beringen has been working with the Beckhoff experts since 2011 and was one of the first XTS customers. No other manufacturer in the packaging industry has implemented as many XTS applications as Syntegon.
Paper packaging is a real sustainable solution in flow wrapping. The retrofit-kit paper-ON-form for existing and new horizontal flow wrapping machines allows the transition from conventional plastic to paper-based packaging solutions – without compromising on speed and production efficiency. The cold sealing technology in flow wrappers enables heat-sensitive products, such as bars and chocolate, to wrapped in paper.
Modular baking systems in flow wrappers feature a modular design, enabling flexible reactions to future needs. The machine can be configured to match product requirements, pack size, and material characteristics – as key factor when packaging products that are variable in shape and texture, such as cupcakes. With this future-proof modular concept in flow wrappers, production capacities can be scaled up, and automation levels increased.
Easy operations with an all-round flow wrapper packaging system feature robust frame construction for stable belt tracking and easy maintenance. The design of flow wrappers provides an improved hygienic design and easy cleaning processes, crucial when processing sensitive products like bars, biscuits, and baked goods. Additionally, the new HMI in flow wrappers supports operators with instructions for daily operations and communicates real-time information about the machine and line status, as well as instructions for upcoming maintenance.
Starting at entry-level, the Pack 103 is a multi-talented, horizontal flow wrapping machine for entry-level lines. With an output of up to 175 packages per minute, it is the ideal companion for startups and medium-sized companies taking their first steps in automation or needing a flow wrapper for smaller batches. The wide format range of this flow wrapper machine can flexibly process various products such as bakery items, bars, biscuits, cookies, and crackers. We support you at every level and help you keep your costs low with these flow wrappers.
Reliable hermetic packaging in flow wrappers is crucial when in need of highly reliable and tight sealing. The HML is suited for the hermetic packaging of various pharmaceutical products such as vial cards, pens, or inhalers. This horizontal flow wrapping machine creates tight seals either with heat or heat ultrasonic technology. Its open machine design enables quick line clearance, thus ensuring high process safety at an output rate of 200 to 250 packages per minute.
System integration in flow wrappers is backed by our long-standing experience in system integration, supporting the successful implementation of your ideas and visions. Our seamlessly integrated systems, including flow wrappers, benefit from coordinated components, tailored specifically to your requirements. Together, we develop a customized solution for your horizontal packaging processes, including product distribution systems, feeding solutions, horizontal flow wrapping, and secondary packaging. A uniform control platform for the entire system, including flow wrappers, ensures optimal operations and contributes to a high overall equipment effectiveness (OEE). From entering the packaging process until your products are transported to supermarket shelves, we have got you covered with our flow wrappers.
Only the right combination of temperature, pressure, sealing time and film type will deliver reliable seals for flow wraps. Additionally, the respective packaging style and product are key factors when deciding for a sealing technology. To master this challenge, we assess your requirements and identify the ideal solution for your product. On request, our test laboratory in Beringen, Switzerland, will carry out extensive tests before you decide on a sealing technology. Our experts are happy to consider the following options with you:
Sensitive food products and film packaging go together like a horse and carriage – or rather they used to. Times are changing, and so does the material that products are wrapped in. Today, even oily and sensitive products like chocolate and baked goods can be wrapped in recyclable mono-materials or paper-based alternatives. Our retrofit kit paper-ON-form processes different types of barrier-paper as well as conventional packaging materials on the same machine, which allows switching materials on the fly. Thanks to our Amplified Heat Sealing (AHS) technology, you can also create tight packs with recyclable, but heat-sensitive mono-material films.
Crackers, cookies, or granola bars require an attractive presentation in supermarket shelves. The flow wrapping materials and packaging design should match the product and brand image. With our horizontal flow wrapping machines, you can customize your design according to your individual product requirements. Whether you want opening aids, hermetically sealed packaging for sensitive products or hot and humid climate zones, or flow wraps with Euro holes that can be hung on racks – our experts will find the right solution for you.
Automation helps with labor-intensive packaging steps, especially when headcounts are small and product safety is a priority. Flow wrapped packs protect the product from environmental influences at low cost. They offer lots of options in terms of brand recognition: different materials and packaging designs convey brand values and high product quality. With up to 175 products per minute, entry-level machines already deliver a significantly higher output than manual packaging. In addition, it avoids direct contact between operator and product, thus improving product safety.
Young and innovative, fast-growing companies often need to adjust their production needs to ever-changing markets and be able to scale up their production output quickly. Expanding their production and packaging facilities must be carefully considered though. The packaging system must be flexible to accommodate a variety of products and packaging formats. It is important to invest in reliable, future-proof technologies that are easy to operate and clean and ensure optimal resource efficiency. Our experts support you in adapting your production lines and service contracts to your individual requirements. Together we work on achieving your production targets quickly and efficiently.
Established companies looking to increase their market share, need to adjust their processes to changing requirements. With Syntegon, they benefit from fast changeovers for different products and package configurations, and quick and easy cleaning processes to avoid contamination. Our systems can be seamlessly integrated to function as a single unit – which makes your production more efficient and ready for industry 4.0. All interfaces are harmonized and the machines communicate with one another. This allows the system to autonomously regulate itself and ensures continuous product flows. The result: reduced downtimes and higher output.
Find out more about our Service Agreements here.
Find out more about Digital Solutions here.
Find out more about Parts here.
Find out more about Maintenance here.
Find out more about Technical Support here.
Find out more about Modernizations here.
Find out more about our Training here.
Find out more about our Expert Services here.
Processing and packaging for a better life – this is what our employees work for every day. Looking back on a 160 years of experience, the portfolio of intelligent, innovative and reliable solutions help our customers in the global pharmaceutical and food industries to improve people‘s life. With 1,100 service experts and a comprehensive service portfolio throughout the entire machine lifecycle from spare parts management to digital line optimization, Syntegon lays the foundation for smooth production processes for all customers.
Visually appealing, cost-efficient, and extremely flexible: flow wraps are the all-round solution for packaging food products.
Snack Connection, a leading Netherlands-based manufacturer of nuts, kernels, and seeds, has partnered with Syntegon to implement a customized packaging solution that boosts efficiency and ensures future-ready production.
Visit us at this year's Vitafoods in Barcelona, May 20-22, at our booth 4B23 and learn more about...
Learn more about our sustainable coffee packaging solutions.
Uncover the secret to visually stunning biscuits, cookies, and crackers. Our site highlights the...
Horizontal flow wrapping is the process of creating a horizontal bag from a single roll of film. Both ends of the film are sealed with either hot- or cold-sealing technologies to form pouches. The flexible packaging equipment that provides bagging solutions across various product sizes. The packaging is very flexible which allows manufacturers to wrap a variety of products, such as cookies, biscuits and bakery goods, confectionery, snacks or even medical devices. Horizontal flow wrapping machines are versatile, catering to both food and non-food applications with customized packaging services. In summary, horizontal flow wrapping is a sophisticated, adaptable, and efficient packaing method that plays a crucial role in modern manufacturing, providing safe, durable, and consumer-friendly packaging solutions.
A horizontal flow wrapper operates as an automatic machine, performing form fill and fin seal processes to package products efficiently. The wrapping speed of a horizontal flow wrapper varies, with some models boasting rapid production rates to meet high-demand packaging services.
Horizontal Form-Fill-Seal equipment produces a pouch or flow wrap, then fills, and seals it in one continouous motion. It forms a bag around the product and seals it on both ends, providing versatile packaging for wide array of items. The material travels through the machine in a horizontal direction. Combining the three steps of HFFS optimizes the total cost of ownership (TCO) and allows for more flexibility in packaging sizes and formats.
The most important requirements are easy accessibility and clear visibility of components. Visibility ensures efficient cleaning processes, while accessibility helps cleaning and sanitizing production facilities. The design should allow for easy and quick disassembly and reassembly of belts, rollers or scrapers, particularly for parts that contact product residue, to maintain hygienic standards. With our machines, all parts that are in contact with product residue can be removed quickly without using tools – this ensures spotless machines.
Different distribution and feeding solutions are available to ensure gentle and hygienic product handling. To prevent product breakage in packaging applications, horizontal flow wrap equipment integrates advanced feeding and distribution systems. These systems, including buffer mechanisms and robotic handling, ensure products are managed with care throughout the wrapping process. The solution range from row distribution to robotic solutions to give systems a wide flexibility and to comply with all different product types in the bakery segment.
Whenever possible in terms of product protection, we recommend paper-based solutions as eco-friendly options for packaging materials. Latest barrier paper developments can be recycled in paper wast stream and offer higher barrier protection at the same time. This makes is a suitable for sticky or oily-baked goods. For products needing higher barrier levels, such as cakes or soft cookies, mono-polyolefin plastics is a fully recyclable and more sustainable packaging material. These mono-materials can be made from PE (Polyethylen), PP (Polypropylen) or even a combined solution.