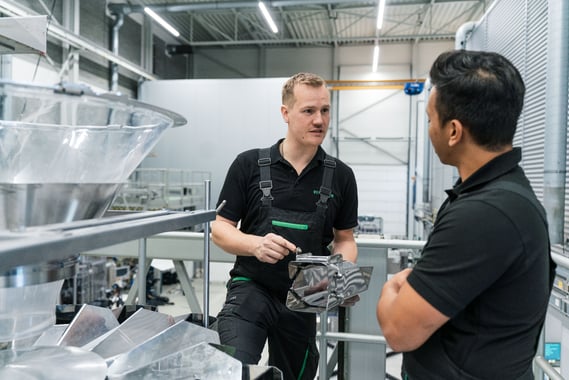
Service Agreements
Find out more about our Service Agreements here.
Automation in packaging is a fast growing trend. Especially during the Covid-19 pandemic, many manufacturers started replacing manual work steps by fully automated packaging systems. This is where pick and place robots excel. They help food manufacturers to reach their production targets at high efficiency and packaging quality levels.
Whether you are automating your product handling to feed a single packaging machine or automating a complete line – our robotic packaging systems competence makes the automation process easier for you.
The Syntegon robotic packaging RPP platform offers outstanding modular scalability with a compact footprint. Its reliable performance reduces downtime, provides high product quality, and enables you to react quickly to changing market requirements. The combination of high OEE, cutting-edge robotic packaging systems, and a compact footprint provides maximum output per m2.
Smart interfaces increase performance with additional robot capacity. A basic robotic RPP configuration consists of two delta robots with a performance of up to 120 picks per robot per minute. The modular design and layout flexibility enable you to scale up step-by-step to grow your production operations.
The robotic packaging RPP platform features a new product belt design with self-tracking and automatic tension control function. Its vision-guided product detection ensures precise product handling, feeding, and product loading operations, or the assembly of variety and assortment packs.
We have designed a new flexible carton and tray transport module to extend robotic product loading options. The 4 or optional 5 axis delta robots pick the products and place them in trays, cartons or infeed chains, either flat or on-edge.
End-of-arm click systems with overload supervision enable fast and tool-less format changes. The new indicator status light concept communicates clear machine status messages to the operator.
The robotic RPP platform's stainless steel, self-draining and IP65-compliant construction provides for hygienic operations. The clever integration of the vision system and other components into the electrical cabinet makes the overall design of the RPP cell clean, open and easily accessible.
A US-based customer produces toaster pastries. They were looking to further automate their production by removing manual operations from the packaging process.
The customer for this project is a US-based industry leader in developing and producing a variety of bakery products for businesses.
The customer is a US manufacturer of organic, plant-based food and ingredients.
This US-customer is specialized in producing frozen French toast sticks for businesses.
Robots replace repetitive manual work while operators may focus on other, more important tasks. With more automation and less hands touching the products – less contamination will happen during the packaging process. As a result, food safety will increase. Robots provide you with maximum performance per m2 floor space in a 24/7 manufacturing/packaging operation.
The maximum pick rate per single robot arm is 140 picks per minute.
At Syntegon, we use 2D and 3D inspection technology. The Syntegon 2D inspection technology is standard. It detects the exact position of randomly oriented products on the infeed belt and conducts 2D-quality checks. Syntegon uses a 2D HD-color vision system. The 2D inspection system also identifies when products on the belts are touching.
Optional, a 3D vision inspection system is available. It is AI-based to enable advanced machine learning. The system checks all products in a 3-dimensional way and rejects faulty products automatically from the packaging process. Based on the statistic system data potential problems in the upstream process can be recognized quickly.
Optional, a 3D vision inspection system is available. It is AI-based to enable advanced machine learning. The system detects the position, shape, size, color and impurities of all products on the infeed belt. The 3D vision system compares the trained images with the actual products. Deviations from the norm are measured and judged good or bad. Good products will be picked, bad products remain on the belt and will be discharged automatically. Based on the statistic system data potential problems in the upstream process can be recognized quickly.
Syntegon RPP robotic pick and place lines come with one or more vision cameras per cell. The definite number depends on your process width and the desired resolution of the images. For vision guided robot kinematics, at least one camera is located at the infeed to check quality and location of the incoming products. Depending on the number of robots and robotic cells, more vision cameras can be installed. Products should be detected nearby the correlated robot, so displacement during travel on the belt has no impact on the quality of the final package.
The Syntegon robotic RPP platform is designed according to hygienic principles:
The standard robotic RPP platform can be cleaned with city water pressure. Other upgrades such as wash-down-robots to achieve full wash-down capabilities are available. Take a look at the graphic to learn about the chemical resistance of the RPP's stainless steel construction: Using robots to satisfy the strictest hygienic requirements (syntegon.com)
Robots replace repetitive manual work while operators may focus on other, more important tasks. With more automation and less hands touching the products – less contamination and product breakage will happen during the packaging process. The vacuum is controlled and applied in a gentle and energy-saving manner. As a result, food safety will increase and product waste will be reduced. Syntegon developed a broad range of end effectors: vacuum-grippers, soft robotics, air-flow-tools, mechanical grippers and more.
Syntegon developed a broad range of end effectors: vacuum-grippers, soft robotics, air-flow-tools, mechanical grippers and more. Our RPP delta robots allow for up to five servo axis kinematic for grouping, tilting, rotating or other operations. Special applications such as reflex-end-of-arm tools provide single-pick-multi-place or multi-pick-single-place handling.
Yes, we have decades of experience in integration of robots into the packaging process. Please go to the contact button on this page to get in touch with us. We will be happy to show you application examples of different projects and to consult you on your specific robotic packaging and handling requirements.
Find out more about our Service Agreements here.
Find out more about Digital Solutions here.
Find out more about Parts here.
Find out more about Maintenance here.
Find out more about Technical Support here.
Find out more about Modernizations here.
Find out more about our Training here.
Find out more about our Expert Services here.
Flexibility was key when developing the Robotic Pick & Place (RPP) platform. Instead of just integrating robots, we took a more holistic approach and brought in all of our industry and robotic application expertise. Syntegon offers you complete automation packaging systems that perfectly fit your project – all from a single supplier.
The robotic RPP platform is our answer to today's automated packaging needs. It combines Syntegon's wide industry know-how with robotics expertise. RPP offers just the right scale, performance, and flexibility our customers need to build as they grow.
The Syntegon robotic packaging RPP platform features a completely modular design. It can be configured according to customer needs and enables a large range of pick and place applications. Delta robots and other modules can be seamlessly integrated into an overall system, allowing our customers to automate single process steps consecutively.
Snack Connection, a leading Netherlands-based manufacturer of nuts, kernels, and seeds, has partnered with Syntegon to implement a customized packaging solution that boosts efficiency and ensures future-ready production.
Visit us at this year's Vitafoods in Barcelona, May 20-22, at our booth 4B23 and learn more about...
Learn more about our sustainable coffee packaging solutions.
Uncover the secret to visually stunning biscuits, cookies, and crackers. Our site highlights the...