In our interview series "Inspection around the world" we take a look behind the scenes of inspection at Syntegon. Behind each machine stands a team of experts – Jose Müller, Inspection Expert is one of them. He develops illumination systems that are used worldwide in Syntegon's automatic inspection machines (AIM). In this interview, he talks about being with the company for more than two decades, cultural diversity and changing responsibilities.
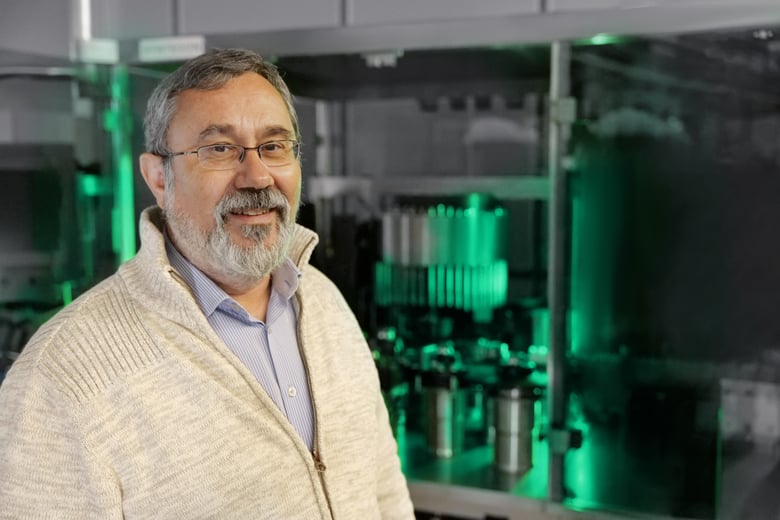
Change keeps the job exciting
In our interview series "Inspection around the world" we take a look behind the scenes of inspection at Syntegon. Behind each machine stands a team of experts – Jose Müller, Inspection Expert is one of them. He develops illumination systems that are used worldwide in Syntegon's automatic inspection machines (AIM). In this interview, he talks about being with the company for more than two decades, cultural diversity and changing responsibilities.
Jose, you are part of a professionally diverse team. In addition to mechanical engineers, your colleagues are, for example, chemical and process engineers or physicists. You yourself are a trained radio and television technician, but now you oversee electronics and software development at Syntegon. Can you tell us more about your career path?
Jose: I have always been interested in technology, even as a young boy. One of the key experiences of my childhood was a visit from a "TV doctor". A technician in a white coat came to our house to repair our television. He hit the set once – and the screen promptly worked as intended again. That made a deep impression on me as a child. At that time, I thought to myself: I want to be able to do that, too! Ever since, I wanted to become a developer. I was interested in working from an interdisciplinary perspective early on. So, I quickly followed up my first apprenticeship with qualifications in quality management, electronics and hardware development, and programming. All these skills came in handy in my first job for Syntegon – at that time still Eisai Machinery. I helped develop the HMI software, electronics and documentation for our automatic inspection solutions as an external service provider in 1997. Two years later, I joined Syntegon.
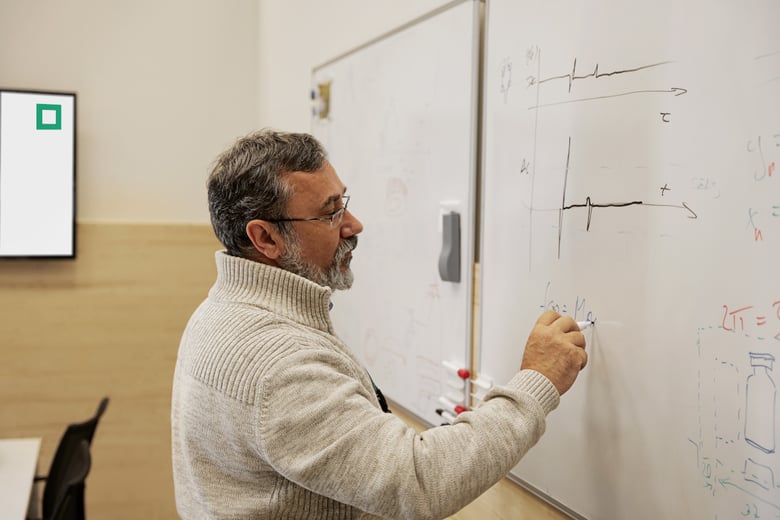
Did you work in development right from the start?
No, in fact I have held several positions during my time at Syntegon – it is this variety that continues to keep my job exciting even after more than two decades. Among other things, I have worked in project management and as a technical manager. As a sales manager I have been responsible for our customers in Portugal, Spain, and Latin America. Today, I take care of the electronics and software of our AIM series (Automated Inspection Machines) together with my team. In particular, we are developing the illumination and camera systems for our inspection machines. I am lucky enough to have an ever-changing workday. There are days when I immerse myself in programming. Other days, I attend customer meetings and collaborate on individual projects. Thus, I can combine my experience from many years in the pharmaceutical industry.
What still makes the pharmaceutical industry interesting for you after all this time?
Quality is a very high priority in our industry. Of course, our customers also want to make a profit, but drug quality and patient safety always come first. Our customers trust our inspection technology to help them produce safe pharmaceuticals. To meet these expectations, our work must comply with high technical standards. I enjoy the professional challenges this poses. In addition, it is very interesting to work with our customers around the world – I get to meet many people from different cultures, which broadens my own personal horizons.
What memory stands out to you after all these years of working with your clients?
It is a great feeling to know that my customers appreciate my work. At the end of the day, that makes it worth it to me. When working together on a project, my customer and I pull together to make it over the finish line. In the past, for example, I had to build prototype systems to meet special dosage form requirements or particularly high inspection standards. When a customer project is that complex, it can happen that the equipment fails the first FAT (Factory Acceptance Test) attempt. All the more reason to celebrate when the test is successful. That has been the case with many of my international customers: I experienced great hospitality in North Africa, Japan, and Brazil. In fact, I liked it so much in Sao Paolo that I could see myself living there for some time.
Why do you like it there?
I have a soft spot for rock, blues and swing and play the guitar and saxophone myself – and Sao Paolo is known for its great music scene. I would love to get to know the culture better and maybe learn to play a new instrument. I am sure that I will manage to keep myself entertained. I am not one to be idle.