In our interview series “Inspection around the world” we take a look behind the scenes of inspection at Syntegon. Behind each machine stands a team of experts – and Kazuya Kamimura, Field Service Engineer in the Production & Service Group, is one of them. He supports customers during set-up of new equipment and inspects and troubleshoots machines around the world. In this interview, he talks about industry trends and his unusual start in the industry.
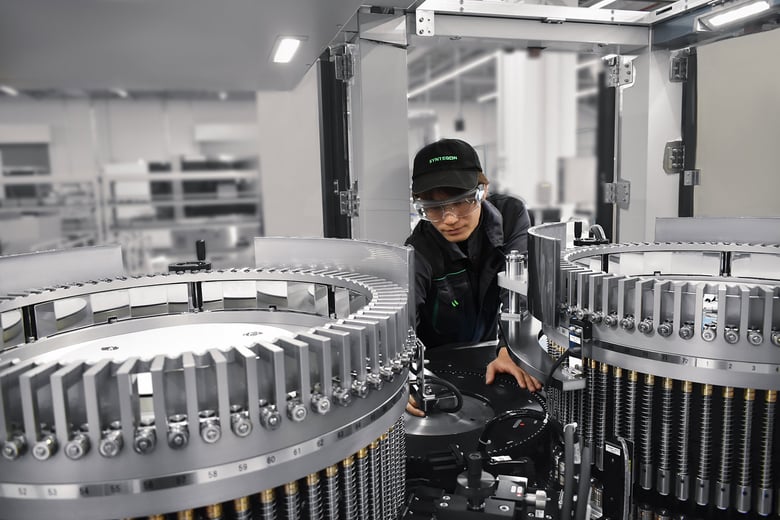
Always at our customers’ side – and sites
In our interview series “Inspection around the world” we take a look behind the scenes of inspection at Syntegon. Behind each machine stands a team of experts – and Kazuya Kamimura, Field Service Engineer in the Production & Service Group, is one of them. He supports customers during set-up of new equipment and inspects and troubleshoots machines around the world. In this interview, he talks about industry trends and his unusual start in the industry.
Kazuya, you have been working as a Field Service Engineer in the Engineering Design Department and the Production & Service Group for 8 years. How did you get your start in inspection?
Kazuya: I first joined what was then Bosch in 2009 as a trainee to participate in the WorldSkills Competition. I was actually working in the automotive business unit when I was offered a transfer to inspection. I took it, despite having no previous knowledge of the pharmaceutical industry as a whole or inspection in particular. Once I started, I quickly began to enjoy it. Inspection is such a crucial step in ensuring the safety of potentially life-saving pharmaceutical products. I’m proud to contribute to that with my day-to-day work.
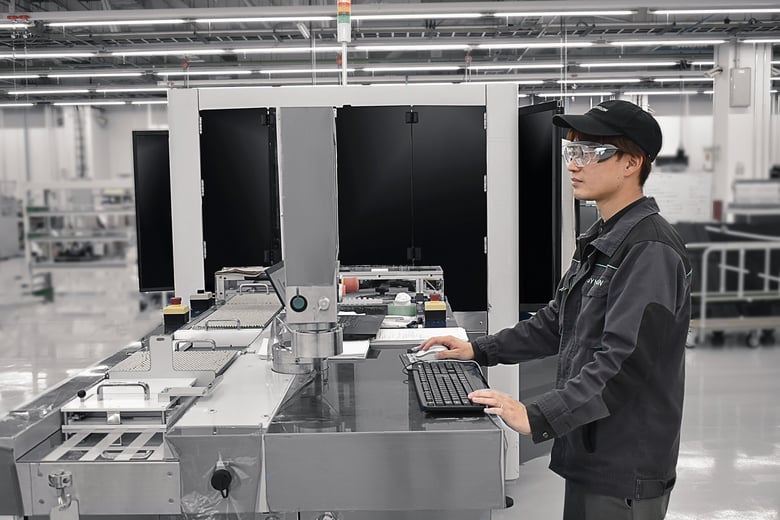
What does your everyday work look like?
Kazuya: I am at our customers’ side throughout the entire lifecycle of their Syntegon equipment. My team and me set up new machines in the factory and install them at the customer’s site. We carry out Factory Acceptance Tests (FATs) and Site Acceptance Tests (SATs) to make sure everything is running smoothly and meeting standards and guidelines. Of course, the actual machines also have a lot of related equipment that we help our customers with – we set up computers needed for operation and monitoring or adjust transportation systems feeding the machines, for example. Later on, we support our customers with periodic inspections and troubleshooting if it’s needed.
That sounds like you have a lot of face-to-face contact with our customers. How important is it for you to know them well?
Kazuya: It’s what enables me to do my best work, really. As a field service engineer, I need to know about customer-specific expectations, requests or requirements and conditions. If you don’t have that kind of information readily available, delays can happen and you’re rushing to meet a deadline – that’s when mistakes can sneak in. Obviously, we want to make sure this doesn't happen. This is why I work in close collaboration with the sales department – for new machine projects, FATs, and SATs – and the service department – mainly for aftersales service. They have already been in contact with the customer when I come in and can tell me all I need to know to best prepare myself.
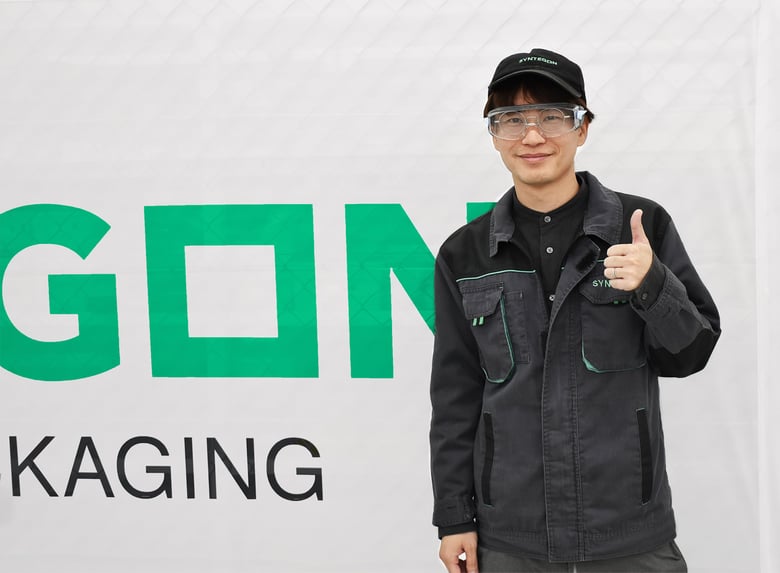
Have you seen a change in customer requirements over the years?
Kazuya: There is a strong trend towards inspection machines that combine multiple inspection process steps in one piece of equipment. Our more advanced machines that include, for example, High Voltage Leak Detection (HVLD), are seeing more demand. In general, I think requirements are getting more complex. This is a challenge for us. On the other hand, projects that push us to get creative and try new approaches as a team often turn out to be quite rewarding.
Speaking of teamwork – inspection at Syntegon is a pretty international affair. What is your experience with working with your colleagues from abroad, like the US and Germany?
Kazuya: This might sound surprising, but I don’t think the cultural differences between us are that big. Sometimes we have slightly different perspectives and sometimes we might struggle with each other’s languages. Any little misunderstandings usually get resolved pretty quickly, though, simply because my colleagues are willing to understand me and vice versa. We are all ultimately trying to make life easier for each other – I think that’s a real testament to our team spirit.