Barrier systems such as isolators or RABS play a fundamental role in the protection of people and products in pharmaceutical production. Only tenths of a millimeter thick gloves are the most crucial interface in these hermetically sealed units. To ensure that barrier systems are sterile, and processes remain safe, a thorough and regular inspection of the glove integrity is vital. The new version of the Annex 1 guidelines, which will come into force in August 2023, also includes requirements for glove testing, in addition to the recommendation of using barrier systems. Hence, many facility operators face the question as to which method is suited best for which system.
Different requirements for isolators and RABS
Gloves for RABS are slipped over the opening for the glove port and removed for cleaning; a manual process requiring special care to not damage the glove. The cleaning of RABS gloves is also performed manually, subsequent sterilization takes place in an autoclave. Since this way of repeatedly handling and sterilizing the gloves have a strong impact on their material, RABS gloves consist of extremely robust and heat-resistant materials such as EPDM rubber.
The high degree of material wear requires particularly thorough testing of RABS gloves to ensure the integrity of the overall system. In fact, the integrity and testing of RABS gloves has increasingly come to the focus of operators over the last few years.
Gloves for isolators are usually cleaned inline as part of the line changeover between two production batches. For this purpose, the gloves remain in their ports, where they are pre-cleaned manually by the operator. The gloves are then also decontaminated during the H2O2 decontamination of the isolator. H2O2-resistant materials such as EPDM rubber or the less cost-intensive chlorosulfonated polyethylene (CSM) are therefore essential for isolator gloves. Since the gloves usually remain in the production line permanently, testing also takes place inline. Ergonomic characteristics and accessibility play an important role to make testing as efficient as possible.
Get inspired with regular updates on technologies and services, case studies, webinar offers and events.
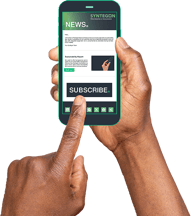
Pressure decay test detects the smallest leaks
The pressure decay test, which was developed by Syntegon at the beginning of the 21st century, ensures a higher reproducibility of the test results. It is the most common physical test method today and can be used both inline for isolators and offline for RABS. For the first time in a glove testing procedure, each glove is stretched several times before the pressure decay test begins. This way all gloves are tested under the same initial conditions regardless of their regular use and utilization rate, which in turn ensures the reproducibility of the test results. The glove system is subjected to a pre-defined test pressure. Here, it is crucial to define the appropriate parameters, leading to each glove type receiving an individually tailored test recipe. Otherwise, a too high or low pressure would risk that damages might not be detected in certain areas of the glove.
Once a certain pressure level is reached, the pressure is repeatedly measured over a pre-defined period. If there are leaks in the glove, air can escape, and the pressure will drop. This method is very accurate and able to detect leaks as small as a few micrometers. The test only takes between ten and twenty minutes, depending on the glove’s material and thickness. Since its introduction about ten years ago, the pressure decay test has become the most common test method in the pharmaceutical industry worldwide. Due to its high degree of reproducibility and testing accuracy, it is particularly suited for regular glove testing.
Glove testing with RFID
With the KHD 3000 wireless glove testing system, Syntegon offers the first test method in the world that can be completely integrated into the production line in accordance with ISO specifications for RABS and isolators. The test parameters can be adapted to the individual glove types. Up to 35 gloves can be tested simultaneously; the measurement data is transferred immediately via Wi-Fi. The filling machine’s HMI controls the system and records all data in the batch reporting, along with all other isolator and filling machine parameters, thus eliminating the need for a separate laptop.
In addition, glove ports and gloves can be equipped with RFID chips. This tracking method ensures that all gloves and glove ports are tested without exception and thus increases the process safety of the testing procedure – especially for lines with several glove ports. The more glove ports are used in a production line, the higher the risk regarding process safety, and the more important the risk assessments and the SOPs of the facility operators. With its flexible solutions, available for both new equipment and for retrofit, Syntegon makes sure that machine operators meet regulatory requirements and deliver excellent inspection results.