Roland Mills United milling group is one of the leading grain mills in Europe. Spread across three locations in Germany, the family-owned company processes more than one million tons of flour per year.
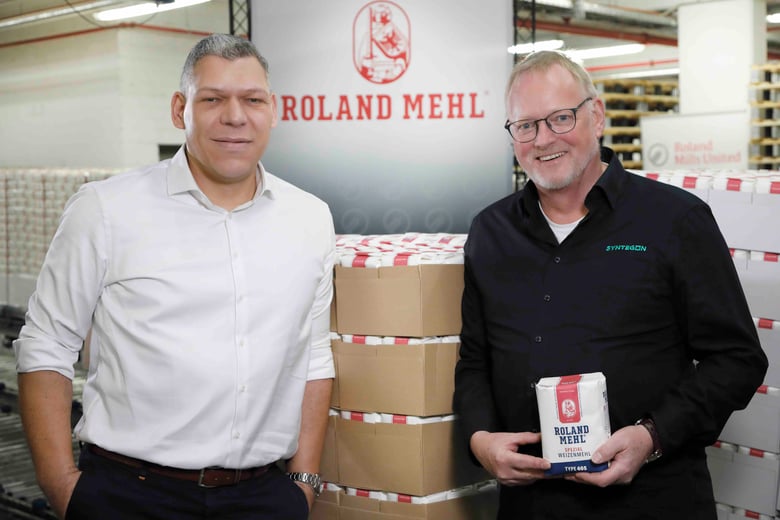
“This packaging offers particularly high quality and is therefore ideally suited for the premium retail sector – a promising market segment for us.”
Future-proof technology with ZAP-module on limited space
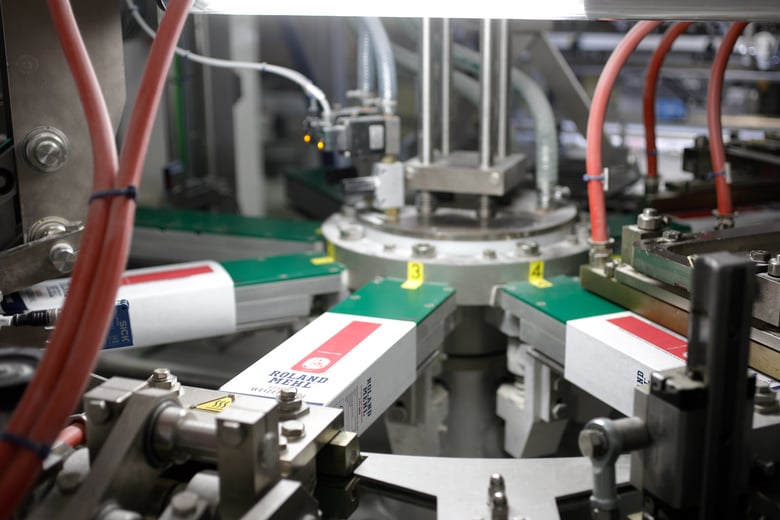
“Our goal was to find a future-proof line solution that combines sustainable primary and secondary packaging. However, this was no easy task, as the line had to fit a limited space. Out of all competitors, Syntegon provided us with the best technical solution and made us feel comfortable. We opted for their Package Maker PME 4081 BS and Elematic 3001 WAH case packer to package our dust-tight flour packs into high-quality cardboard trays.“
Turnkey line solution
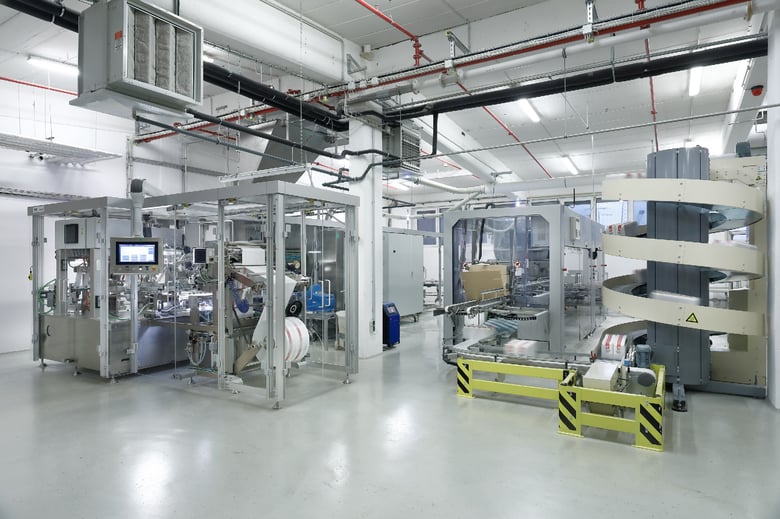
Besides the high machine availability, the experts at Roland Mills United are also impressed by its packaging flexibility.
“Thanks to extensive test runs, we knew that we could process paper from various suppliers on the machine. This gives us an important competitive advantage,” explains Karrenbauer. It was important for us not to depend on a single supplier, but to be able to use different packaging materials in the future – one of the benefits delivered by Syntegon’s Package Maker.”
For Roland Mills United, it was clear from the very beginning that the products’ secondary packaging had to match the primary packaging in quality. The Elematic 3001 WAH case packer from Syntegon packs 100 flour packs per minute – and is particularly sustainable thanks to minimal use of adhesives. When folding the display cartons, the adhesive is only applied selectively so that the secondary packaging can easily be disposed of in the paper waste.