Barrier systems such as isolators or RABS play a fundamental role in the protection of people and products in pharmaceutical production. Only tenths of a millimeter thick gloves are the most crucial interface in these hermetically sealed units. To ensure that barrier systems are sterile, and processes remain safe, a thorough and regular inspection of the glove integrity is vital. The regulatory requirements for gloves are strict. However, they also leave plenty of choice for suitable test methods. Many facility operators face the question as to which method is suited best for which system.
Pressure decay test detects the smallest leaks
The pressure decay test, which was developed by Syntegon at the beginning of the 21st century, ensures a higher reproducibility of the test results. It is the most common physical test method today and can be used both inline for isolators and off-line for RABS. For the first time in a glove testing procedure, each glove is stretched several times before the pressure decay test begins. This way all gloves are tested under the same initial conditions regardless of their regular use and utilization rate, which in turn ensures the reproducibility of the test results. The glove system is subjected to a pre-defined test pressure. Here, it is crucial to define the appropriate parameters, leading to each glove type receiving an individually tailored test recipe. Otherwise, a too high or low pressure would risk that damages might not be detected in certain areas of the glove.
Once a certain pressure level is reached, the pressure is repeatedly measured over a pre-defined period. If there are leaks in the glove, air can escape, and the pressure will drop. This method is very accurate and able to detect leaks as small as a few micrometers. The test only takes between ten and twenty minutes, depending on the glove’s material and thickness. Since its introduction about ten years ago, the pressure decay test has become the most common test method in the pharmaceutical industry worldwide. Due to its high degree of reproducibility and testing accuracy, it is particularly suited for regular glove testing.
Get inspired with regular updates on technologies and services, case studies, webinar offers and events.
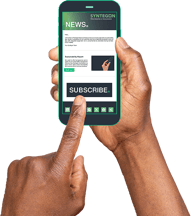
UX-based redesign KHD 2000
KHD 2000 is an off-line glove testing system for independent testing of RABS gloves. The main difference to conventional testing is that the operator tests the gloves outside the production line in a lower classified cleanroom (e.g. class C or D). This allows gloves from multiple RABS lines to be tested simultaneously, reducing downtime at the production line for the operator. During the redesign, the proven technology from the KHD 3000 was adapted for the KHD 2000. Additionally, the testing procedure was revised for ergonomics and ease of use. Customer as well as operator feedback from daily use were included in the redesign process (UX- User Experience).
Glove testing is a customer-specific process based on a risk analysis. To ensure the highest safety, additional testing of critical glove positions can be performed by wireless glove testing systems directly at the production line, in installed condition.
Syntegon offers the full range of glove testing systems
With the KHD 3000 wireless glove testing system, Syntegon offers the first test method in the world that can be completely integrated into the production line for RABS and isolators in accordance with ISO guidelines. The test parameters can be adapted to the individual glove types. Up to 35 gloves can be tested simultaneously; the measurement data is transferred immediately via Wi-Fi. The filling machine’s HMI controls the system and records all data in the batch reporting, along with all other isolator and filling machine parameters, thus eliminating the need for a separate laptop.
In addition, glove ports and gloves can be equipped with RFID chips. This tracking method ensures that all gloves and glove ports are tested without exception and thus increases the process safety of the testing procedure.